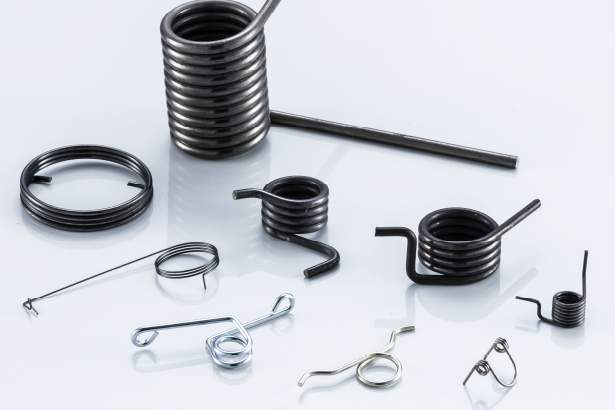
TORSION SPRING
Torsion springsĀ are designed and wound to be actuated rotationally, and to provide an angular return force. They are used in all types of hinges and assemblies such as self-closing doors and lids. There are often many options for leg configuration so the spring can be attached in different ways. The most important size parameters to consider when searching for torsion springs include design units and dimensions. Design units can be specified in English or metric units. Some manufacturers may specify both. Important dimensions include inner diameter, outer diameter, wire diameter, and spring length. The inner diameter is typically specified when the spring is required to slip over a mandrel with sufficient clearance to operate freely. The outer diameter is typically specified when the spring is required to fit into a circular hole with sufficient exterior clearance to operate freely, or if there are outer housing clearance issues. The wire diameter is the diameter of the actual spring wire. The spring length is the length of the spring coil.
Important performance specifications to consider when searching for torsion springs include spring rate, maximum deflection, maximum load, and wind specifications. Spring rate is the angular return torque provided per unit of angular displacement. The maximum deflection is the maximum rated angular deflection of spring before damage. The wind of the torsion spring can be right hand, left hand, or double torsion. Double torsion wind springs have one right-hand and one left-hand wind on the same spring, usually with an unwound section between the winds. The two legs emerge from the spring on the same side. Leg specifications to consider for torsion springs include leg angle, equal leg length, and leg end style. Springs that are straight or parallel on the same side are considered to have a 0° leg angle. Increasing angle is in the unwinding direction. Some legs have equal length. Leg end style choices include straight torsion, straight offset, hinged, short hook ends, and hook ends.
Choices for materials and finish for torsion springs are also important to consider. Common materials of construction include hard drawn steel, music wire, spring steel, stainless steel, other metals, and non-metallic. Music wire is a common and relatively inexpensive high-carbon steel alloy used for spring manufacture. It is cold drawn and offers uniform tensile strength. Spring steel is a standard industrial grade of steel specifically used for spring making. It exhibits good elastic and return properties. Stainless steel exhibits good corrosion resistance for specialty applications. Exotic metals and their alloys with special properties and applications; include such materials as beryllium copper, beryllium nickel, niobium, tantalum, and titanium. Plastic is a broad category including all thermoplastic materials used by custom spring winding service providers. Plastic springs may be used in light-to-medium duty applications for quiet and corrosion-resistant qualities. Finishes include none, black oxide, gold irridite, passivate, and zinc.
Reviews
There are no reviews yet.